Manual Handling: Time for a refresher
Health & Safety Advisor, Lee Garner from Stallard Kane discusses manual handling in the workplace and new legislation.
“Manual handling occurs in practically every workplace and encompasses everything from lifting and supporting a load, through to transporting the load by pushing it, pulling it, carrying it or moving it in any other way that requires physical labour.
Manual Handling injury statistics in the UK
Many musculoskeletal injuries caused by lifting and handling accumulate over time. They are caused by carrying out tasks repeatedly rather than being caused by a single incident. Common injures range from pulling a muscle to damaging tissue, trapping a nerve, crushing vertebrae or causing a hernia. Most injuries are to the back, but hands, arms and feet are also vulnerable to fractures and lacerations.
In the UK, musculoskeletal disorders accounted for 8.9 million working days lost in 2019/20 according to the latest Labour Force Survey (LFS). These latest estimates from the Survey also show that the total number of cases of work-related musculoskeletal disorders in 2019/20 was 480,000, which equates to a rate of 1,420 per 100,000 workers. Generally, manual handling, awkward or tiring positions and keyboard work or repetitive action are estimated to be the main causes of injury.
Of the total amount of cases reported, 19% of these were caused by lower limb injuries, 37% by back injuries and 44% were caused by upper limbs or neck injuries. In relation to the total number of reported cases of work related ill-health in 2019/2020 musculoskeletal disorders accounted for 30% of all cases and 27% of all working days lost due to work-related ill health.
Manual Handling Legislation
Employers have a responsibility to protect their workers from the risk of injury due to hazardous manual handling in the workplace. Employers or employees that seriously breach manual handling regulations potentially face large fines.
The legislation that covers Manual Handling is The Manual Handling Operations Regulations 1992 (as amended in 2002). This legislation requires employers to:
- Avoid hazardous manual handling as far as reasonably practicable. This could be achieved by: Redesigning the task to avoid moving the load, Automating or mechanising the process such as the use of pallet trucks, fork lift truck or a hoist.
- Assess the risk of injury when completing your risk assessment.
- Reduce the risk of injury as far as reasonably practicable.
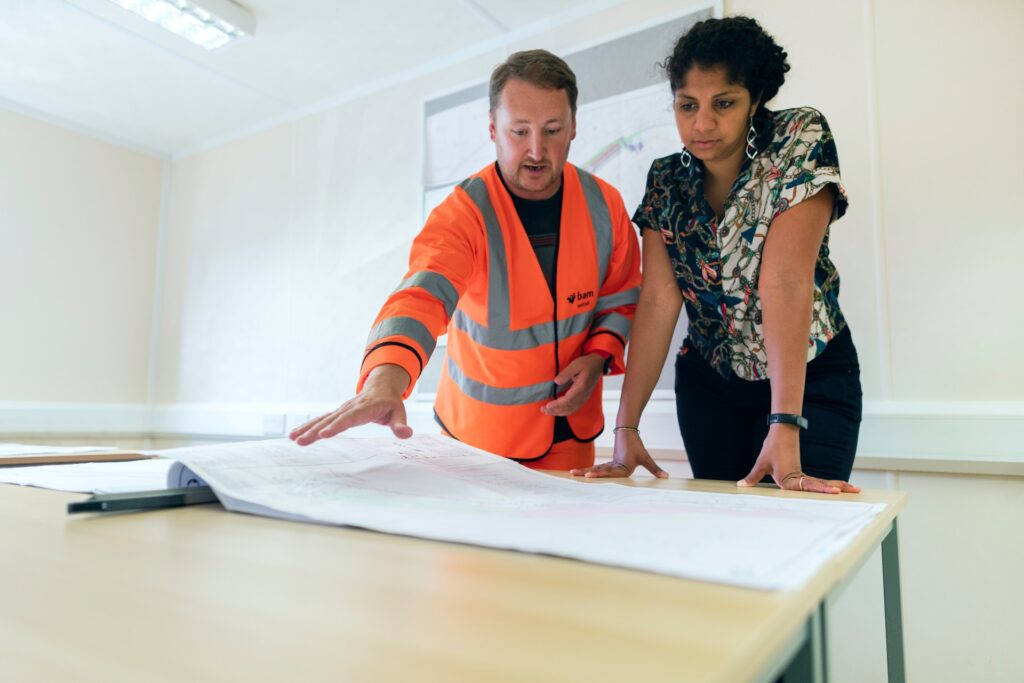
Risk Assessment
It is essential that employers have conducted a suitable and sufficient risk assessment and tried to reduce any risks associated with manual handling. This risk assessment must be communicated to all employees.
Assessing the risk of injury
You should consider four specific areas in your risk assessment – Task, Individual, Load and Environment:
The Task: does it involve twisting, stooping, bending, excessive travel, pushing, pulling or precise positioning of the load, sudden movement, inadequate rest or recovery periods, team handling or seated work?
The Individual: who is the best person for the job considering health, pregnancy, age and other factors?
The Load: is it heavy, unwieldy, difficult to grasp, sharp, hot, cold, difficult to grip or are the contents likely to move or shift?
The Environment: are there space constraints, uneven, slippery or unstable floors, variations in floor levels, stairs or steps, doors to open, extremely hot, cold or humid conditions, poor lighting, poor ventilation, gusty winds, clothing or Personal Protective Equipment that restricts movement?
Reducing the Risk
You can reduce the risk of a manual handling accident occurring by:
- Avoid lifting and handing, by using automation
- Use a lifting aid and make sure these are maintained in full working order
- Reduce carrying distances
- Ask for assistance in lifting
- Plan the lift and provide a clear path
- Break the load down into smaller parts
- Train employees and volunteers in correct lifting and handling techniques
- Make sure you have a good grip on the load, whether lifting, pushing or pulling
- Consider storage height of items to be lifted – lifting below knee height or above shoulder height puts increased strain on the spine
- Provide suitable PPE such as steel toe capped boots and gloves and masks
- Wear suitable clothing that doesn’t threaten to obstruct the lift
Employees should know their limits and be confident to ask for help if needed.
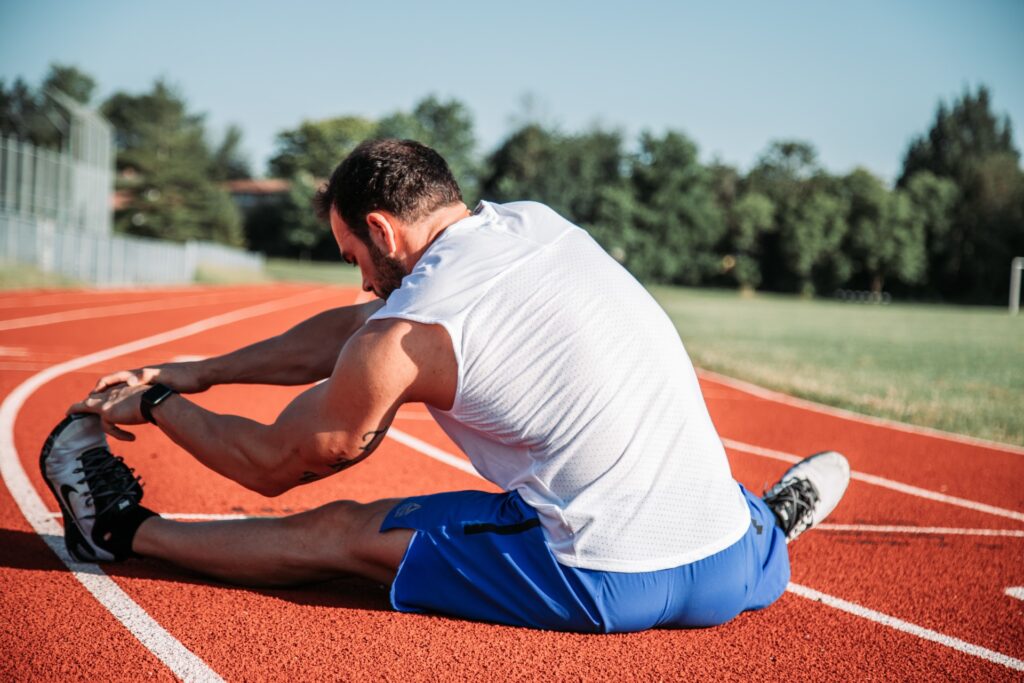
Safe Lifting Techniques
To ensure that no injury occurs when moving a load, it is important that the correct technique is used.
To safely lift a load:
- Place feet hip-width apart with one foot slightly in front of each other
- Moderate flexion of the back, hips and knees
- Grasp the load firmly
- Use the leg muscles to lift the load into a standing position
Whilst holding the load it is important to remember to:
- Keep the back straight, avoiding twisting or bending
- Carry loads with straight arms
- Keep the head up and face straight ahead when handling a load
- Keep the load hugged in close to the body while moving